Lighting.
cast wall sconce - detail
Creating functional parts.
I met Emer who runs Spark & Bell - a local lighting company specialising in handcrafted lights - a few months back in late 2020. Emer and her team were looking for ways to showcase designs and work with local makers and designers. What followed was a series of conversations around developing a series of parts that would go together to form a small collection of unique lights.
It was a relatively open brief, although it was an interesting challenge to design objects that ultimately had to fit with standardised lighting components as well as S&B’s signature brass parts.
After some experimentation, we settled on working with a complementary material pallete of cork, acrylic resin and recycled plastic. Each material can be machined or cast in a way to consistently produce interesting forms that also match the functional requirements of a working lighting piece.
The three core designs - each serves as a base model from which multiple product configurations are possible depending on lighting fixture, mounting position and the addition of various ‘ad-ons’.
ABOVE: exploded view of “Rowan” table lamp
The “Rowan” table lamp fits together with no glue, combining together four parts - a cast base that forms the structure, a milled cork base insert that houses the electrical fittings whilst also intersecting with a contoured cork dish. The lamp is finished with a brass overhead fitting or a flush mounted bulb, depending on the desired model.
All the parts were designed to be assembled at Spark & Bell’s workshop, where each lamp is assembled to order.
ABOVE: CNC machining some of the lighting elements
ABOVE: Moulding, casting and finishing the “Solas” lamp base.
Casting with Jesmonite formed a large part of the processes involved in making this collection, where its versatility in finish and form make it particularly suited to the brief. The colour palette of the series is a simple one - black, white and terracotta - but by using various amounts of waste ‘dust’ leftover from machining other parts of the series, a unique texture was achieved - effectively rendering each individual product unique.
This collaboration also led to me working more intensively with recycled plastic, in particular a type of recycled LDPE that is semi-translucent, naturally lending itself to a lighting project. I want to dedicate a separate blog post to the prices involved as it took a lot of development to perfect various techniques of cutting, heating, bending and rolling to achieve the final fluted “Rian” table light.
More details on the full range of lights can be found on Spark & Bell’s website.


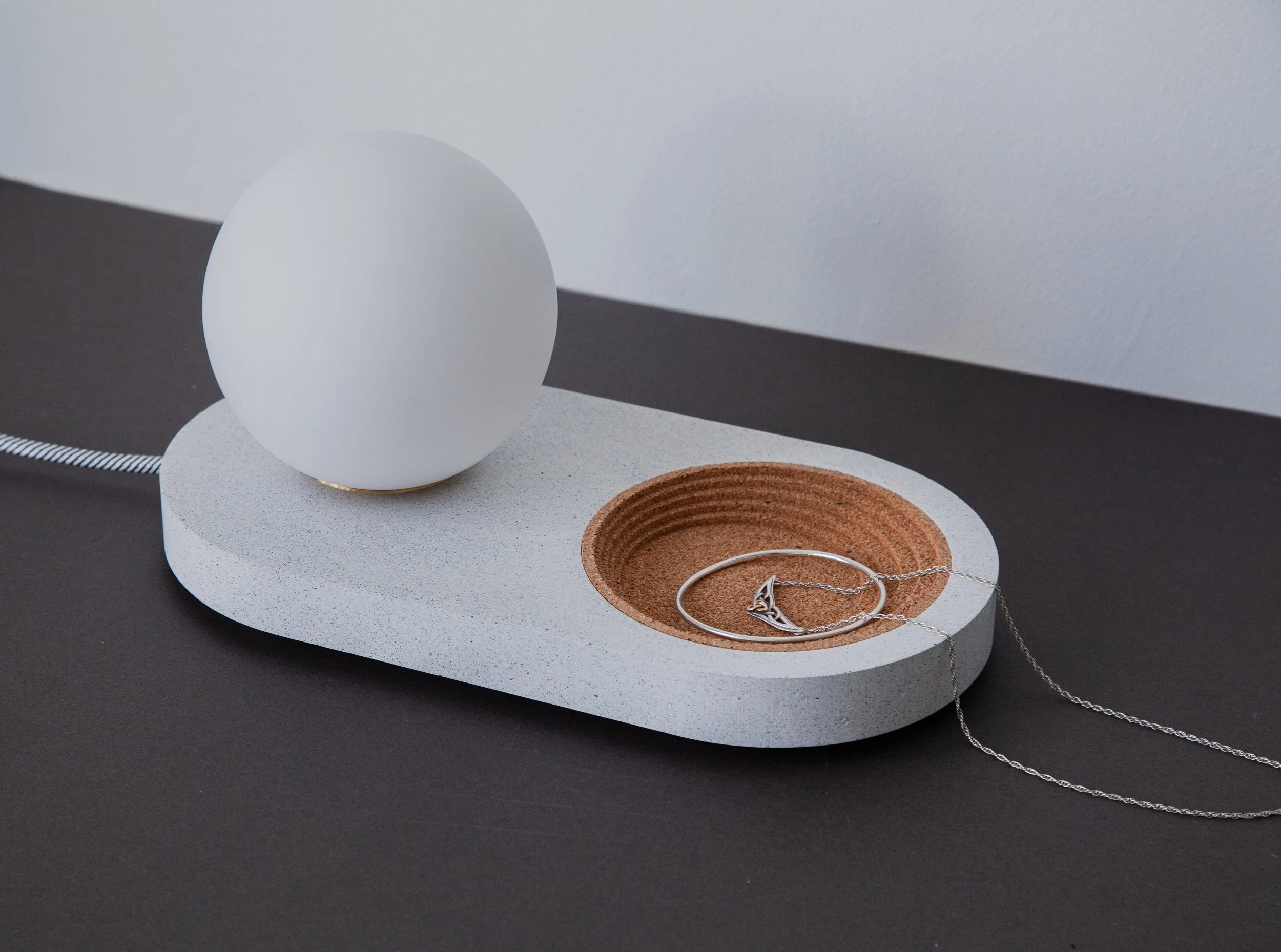

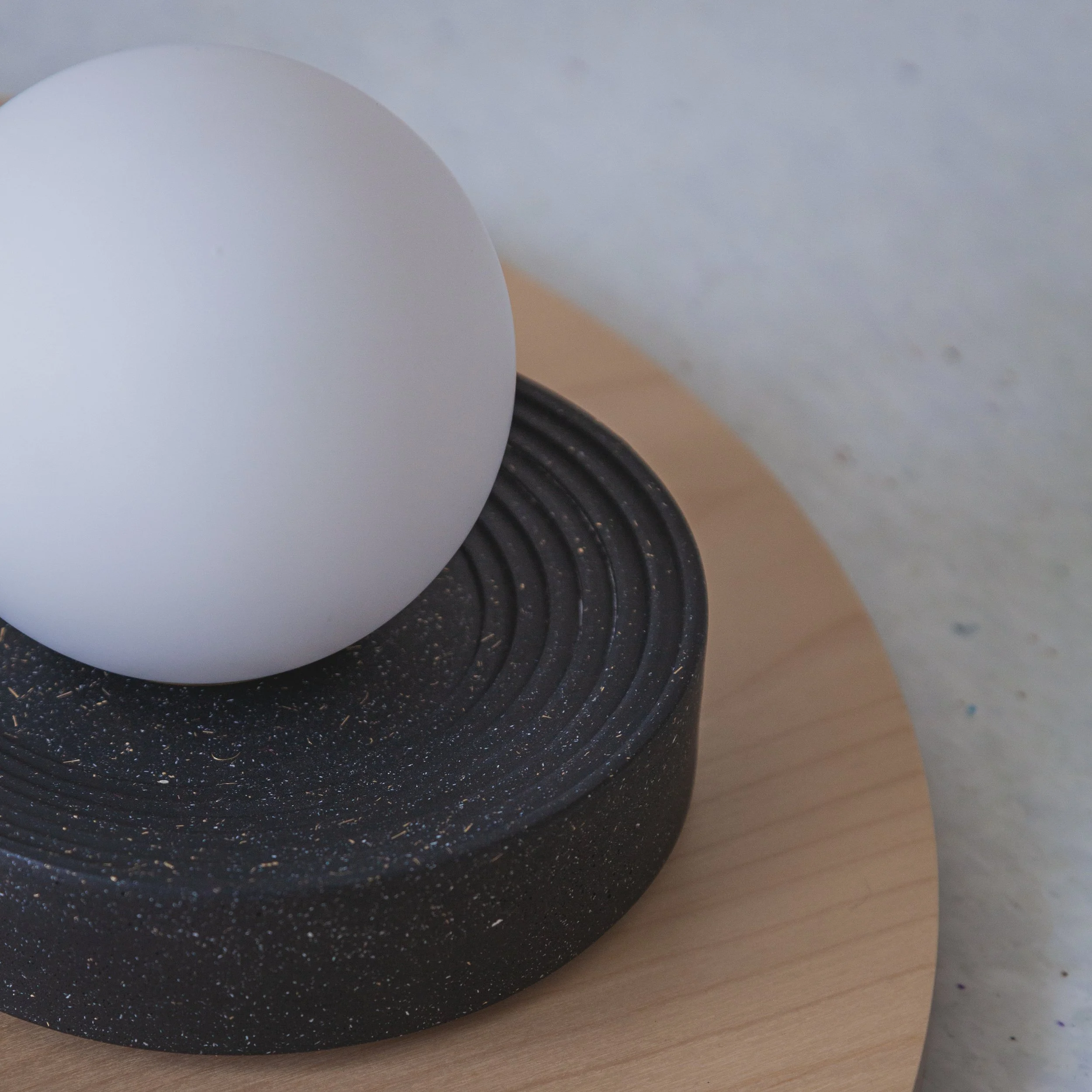

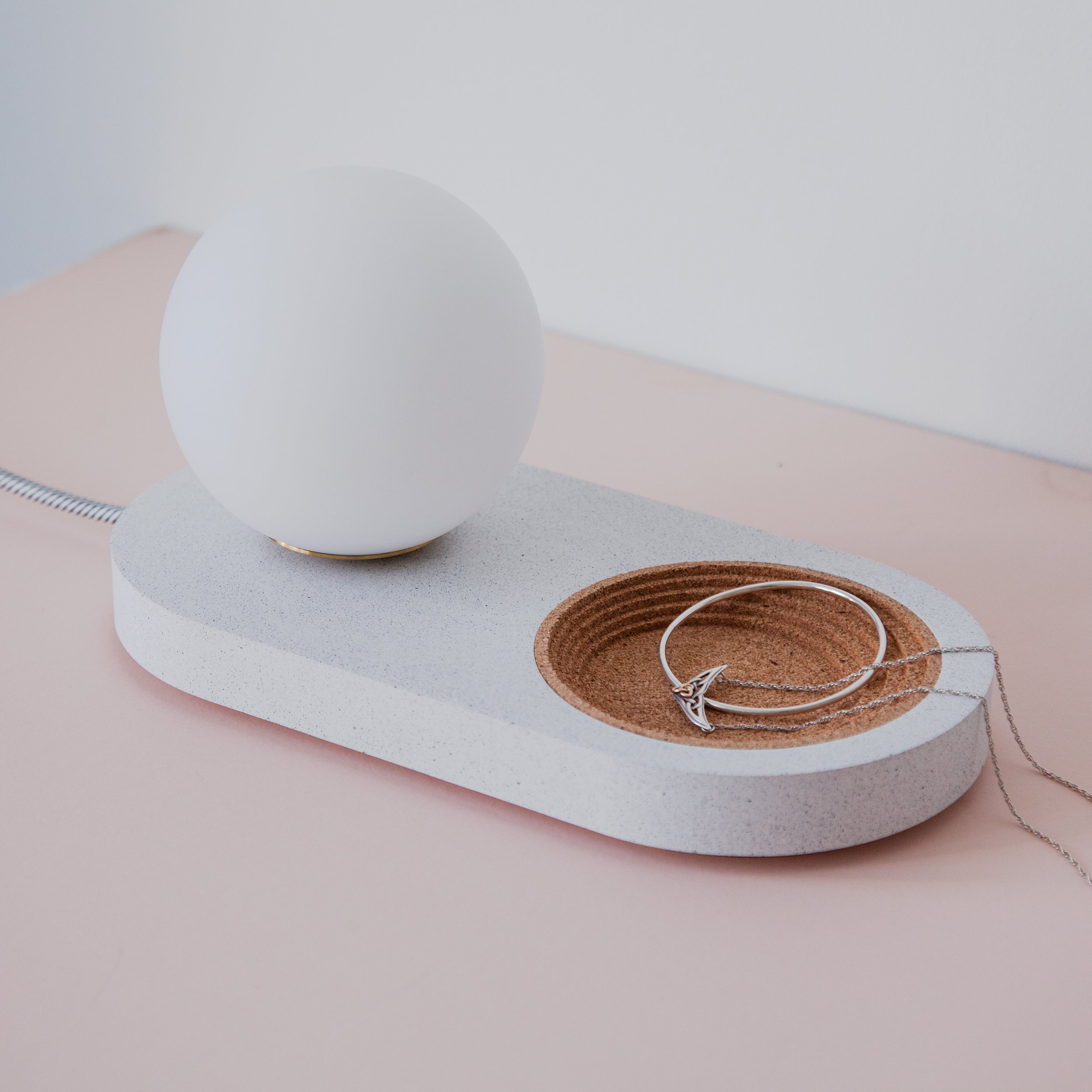



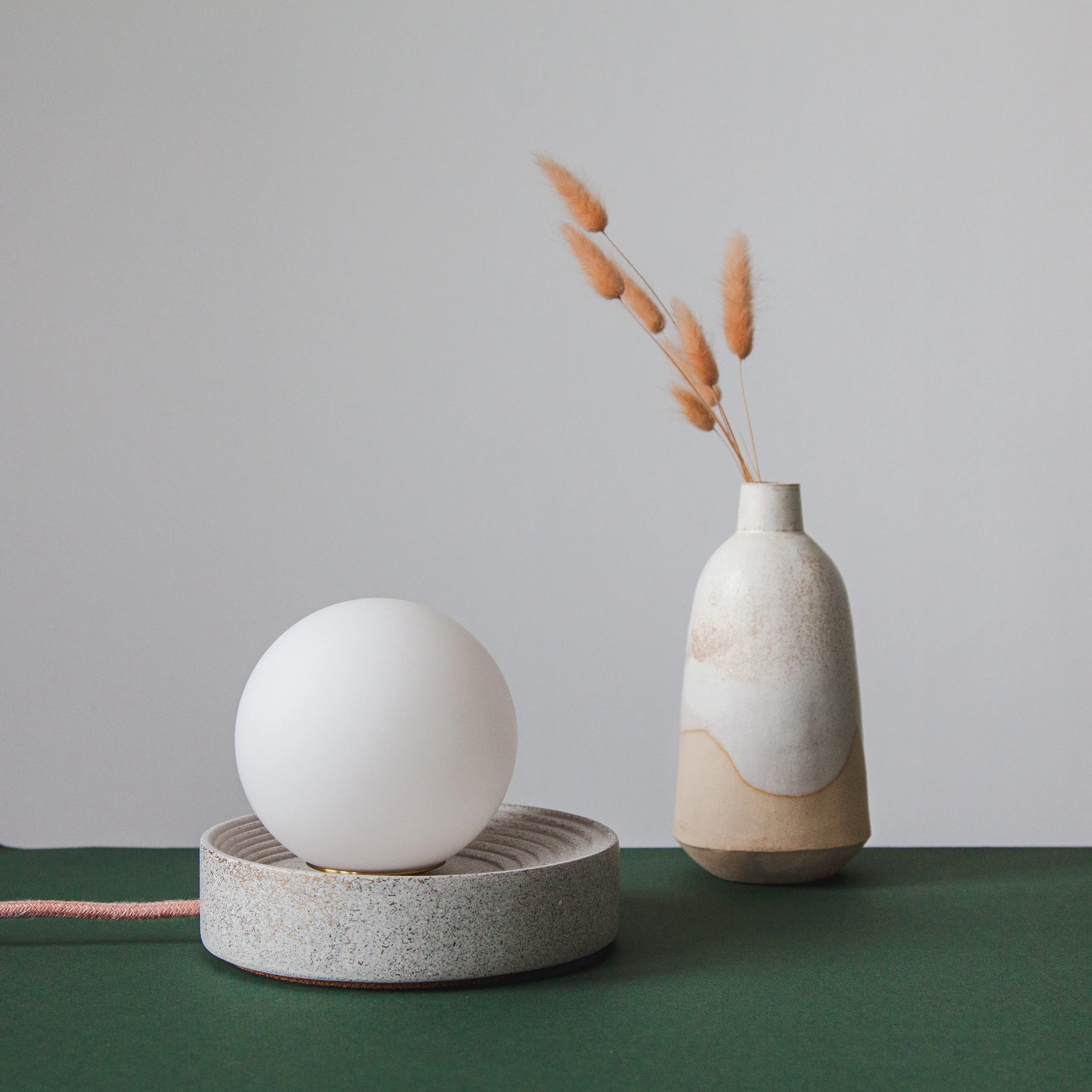



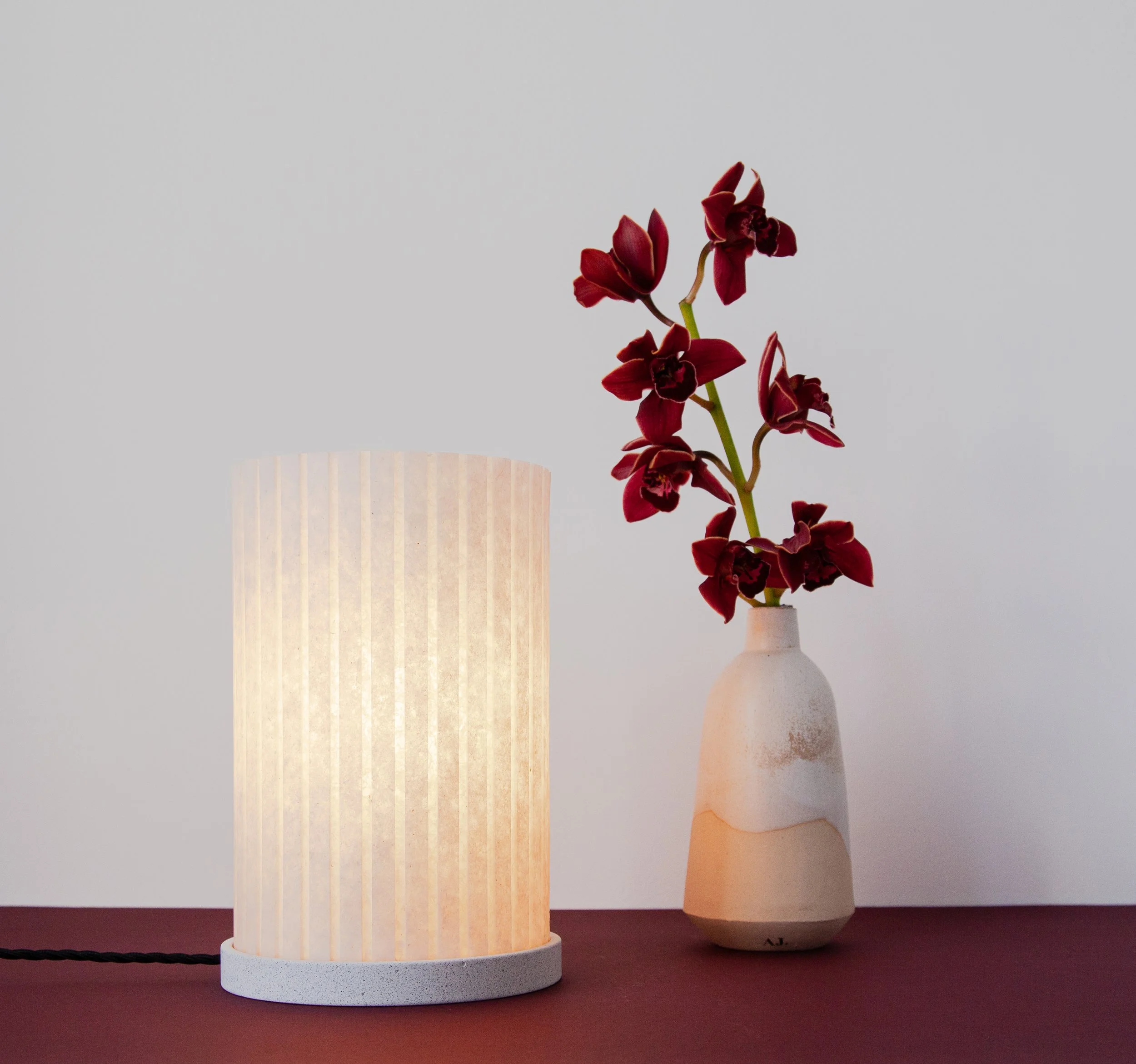

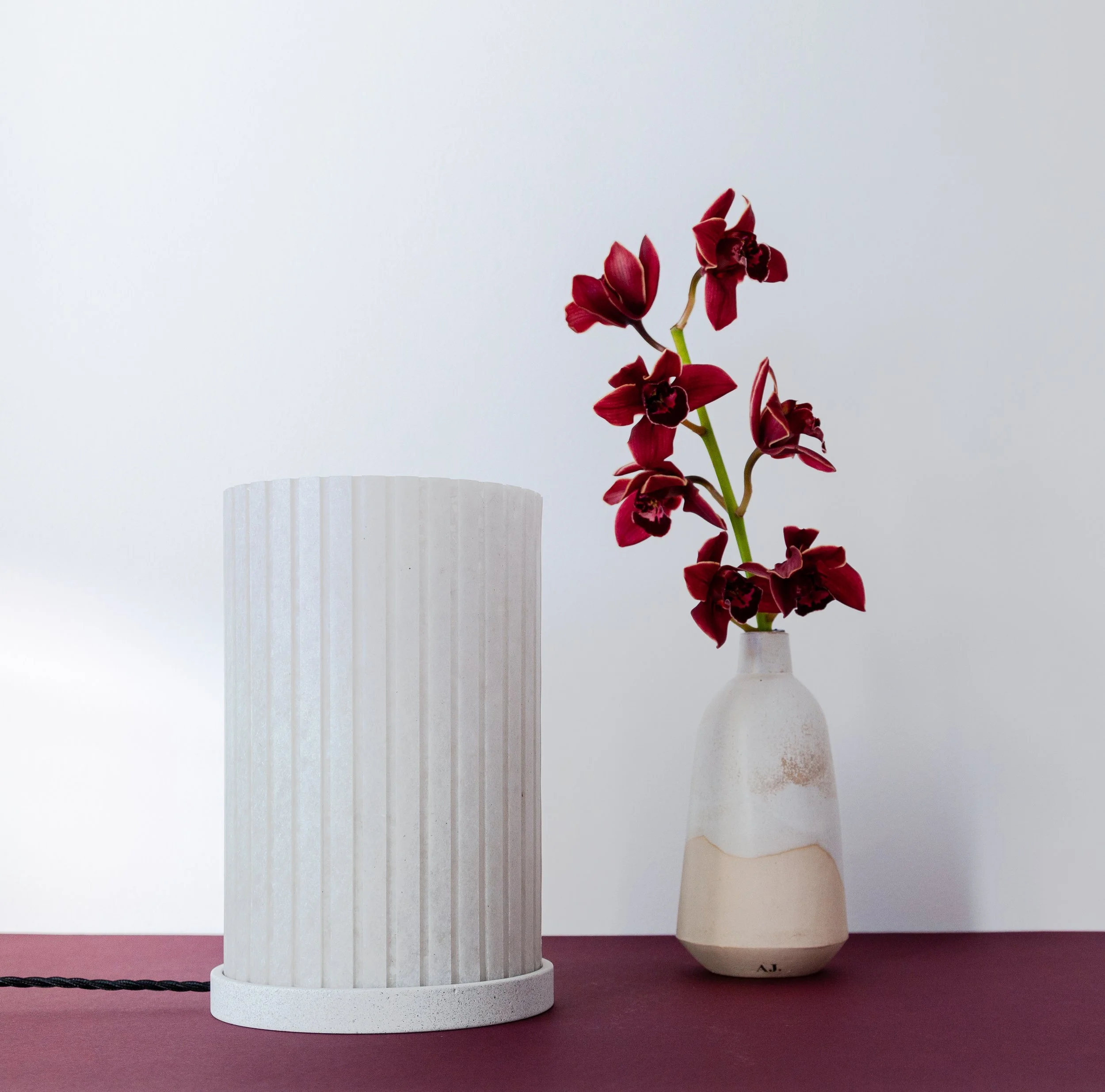


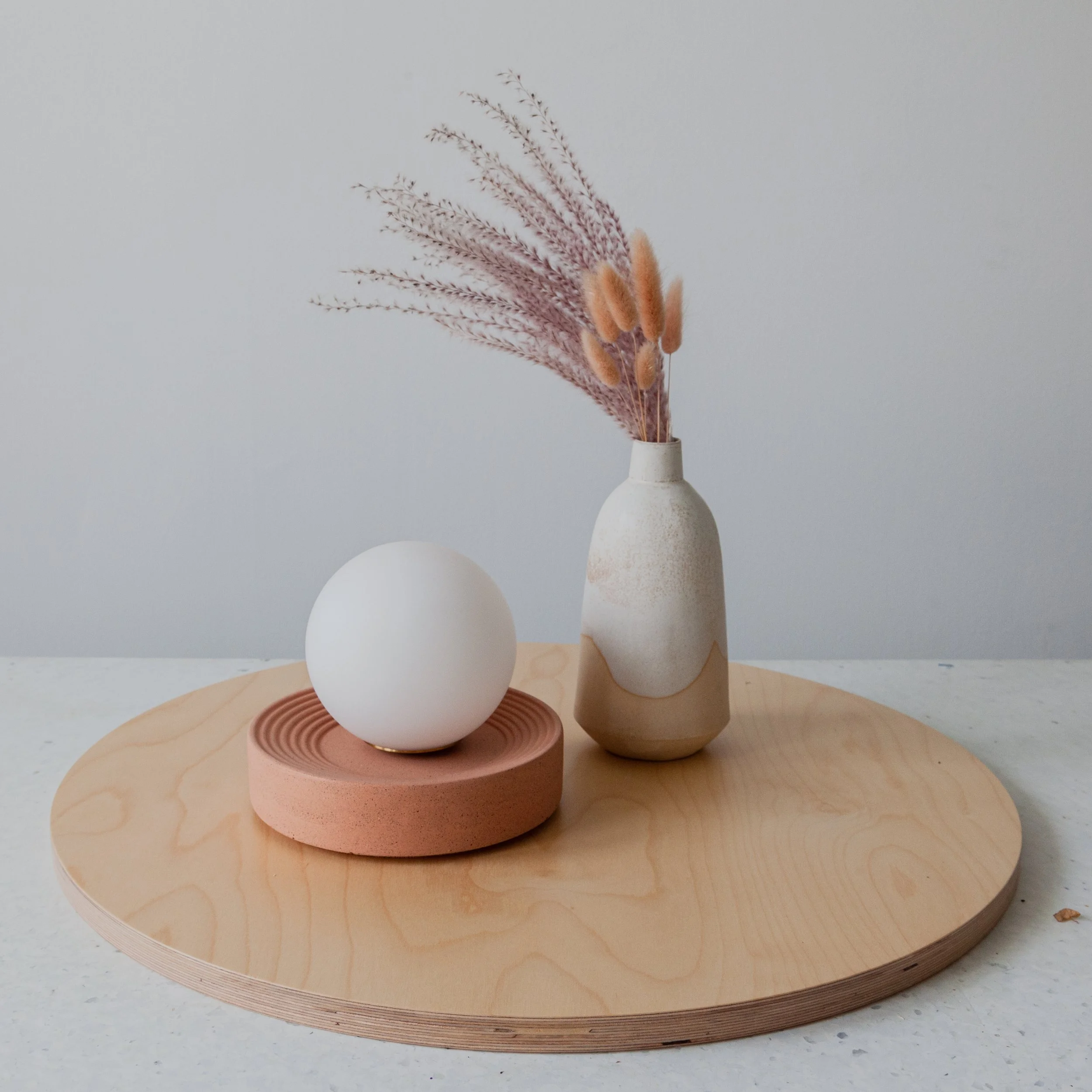